智能硬件产品研发全流程解析,值得收藏!
首先上图,这也是很多硬件工程师找小编要的图片,赶紧保存下来吧!
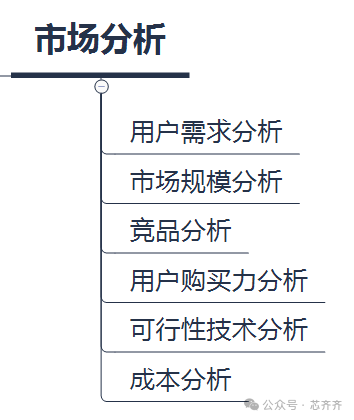
硬件电子产品的独有特性:
资金需求:项目总预算,包含研发、生产、营销等各环节费用。
技术方案:确定软硬件架构、技术栈、云服务选择等。
人员配置:列出项目所需的关键角色与人数。
项目周期:从研发到上市的时间表,包括关键里程碑。
利润预测:基于市场分析和成本分析,预测项目收益。
营销方案:制定产品推广策略,包括线上线下的营销渠道、品牌建设、公关活动等。
产品迭代计划:规划产品上市后的持续改进和版本更新路线图。
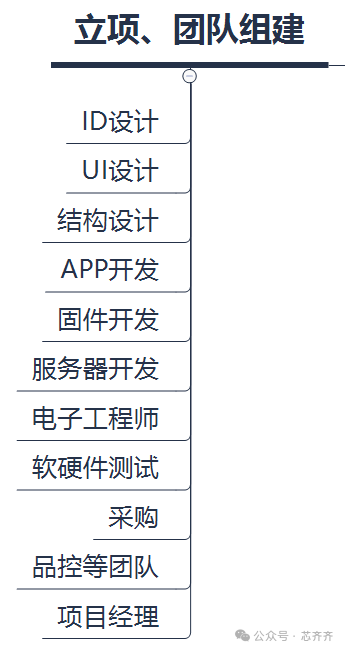
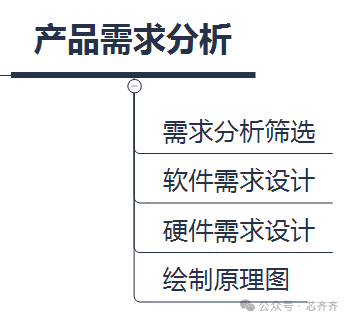
1. 需求分析
2. 硬件需求设计
3. 软件需求设计
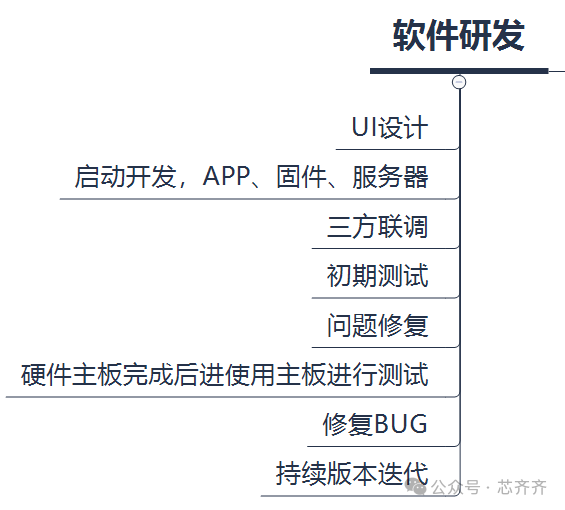
1. 界面设计
2. 软件开发
3. 三方联调
4. 初期测试
5. 修复缺陷
6. 持续迭代
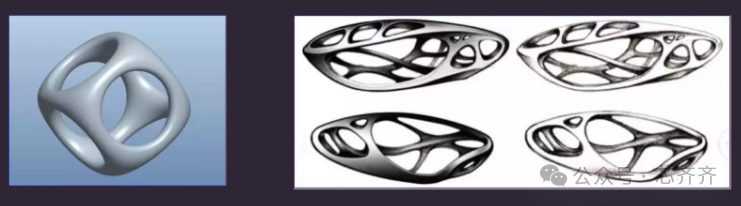
1. ID评审
2. 打手板验证

在结构设计中需要注意根据ID和主板等配件,设计出兼顾两者的内部结构。同时也要考虑产品的坚韧度、组装难度、脱模难度,有运动部件的产品尤其需要注意的是运动部件的结构灵活性和稳定性。
我们之前做的一款产品就曾因运动部件的结构出问题而导致在使用时间稍微久一点或磨具有稍微误差后就会出现阻力增大的问题,最后导致有不少产品进行换货处理,并且曾也增大了模具开发的难度和产品的成品率。
结构设计好后可通过3D打印等技术进行打样拼装,验证其设计如何?
1. 设计内部结构
2. 结构打板验证:3D打印
3. 结构设计封板

在电子设计和开发中需要注意的是PCB设计和电子元器件选型这两个问题。
第一个是PCB设计时要考虑走线、SMT难度、分离模拟电路与数字电路以及元器件和电路之间的电磁干扰等相关问题。尤其要注意干扰问题,因为这样的问题有时是隐性问题,说不定就在什么时候就会出现。倘若在产品生产大规模后出现那可就尴尬了。
第二个是元器件选型的问题,在电子元器件选中要避免使用偏门的,因为有可能这个元器件随时会面临停产或者与其他元器件难兼容,有时更换一个元器件会因为Pin脚或驱动不兼容而带来大麻烦。对于产品来说使用成熟稳定的元器件不仅能提升产品的稳定性,甚至有时还能降低产品的成本。
在主板设计好后即可进行打板出样品了,样品出来后即可烧录固件对其进行测试和优化。
1. PCB设计
2. 电子元器件选型
3. 打板验证
4. 烧录固件,测试优化
5. 输出《电子BOM》
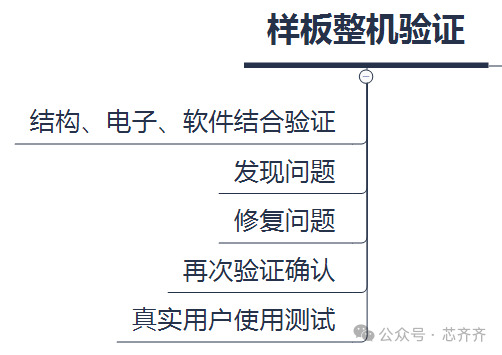
在这个阶段基本APP、固件、电子、结构都已经出了1.0版本了,此时就可将产品进行整机的组装和验证了。
在这个阶段产品除了要进行各方面的测试验证和迭代优化之外,还需要将产品拿到实际的应用场景和用户那里进行使用测试,这一步不仅可以从用户的角度测试产品的性能,还能暴露出产品场景设计和需求以及产品体验问题,因此这一步是非常有必要的,当产品进一步成熟后再发现问题就很难进行修改了。
1. 整机组装和验证
2. 真实场景用户使用测试
在互联网上有很多关于产品经理改需求的段子,而在硬件产品经理圈几乎是没有的。主要是因为硬件产品如果做需求变更的话,那么所需要付出的成本是非常高的。
比如随便开一个模具都是要十几二十万起步,这样高昂的代价谁敢随便需求变更?
再比如对主板进行需求变更,你要知道的是对主板进行一次修改、打板、测试没有个两三周是搞不来的,这样随便搞几个次一两个月就过去,时间这么宝贵谁能经得起这样的折腾呢?
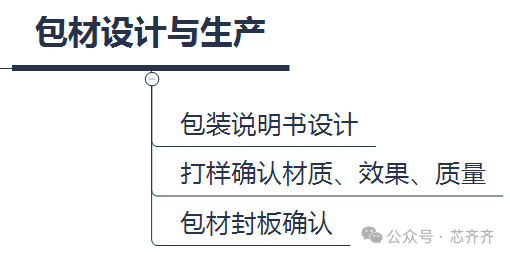
产品在经过上个阶段后基本外观、功能、配置就已经敲定了,所以此时就可以开始进行包装和说明书的设计和生产了。
如果产品还距离量产的时间还长,那么可以在包材设计打样确认后过一段时间在进行生产,以免因长时间存放导致出现问题。
1. 包装设计、说明书设计等
2. 打样,验证材质、效果和质量
3. 包材封板确认
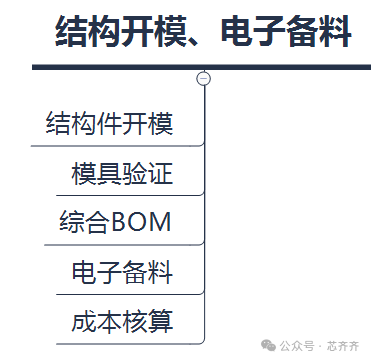
在产品经过多次测试后,若在ID、结构、电子没有需要改动的情况下模具就开始开模了,电子元器件也可以开始备料。通常开模的时间至少需要2个月以上,所在这段时间内就可以继续迭代优化软件。
在开模这段时间里需要产品经理和结构设计师定期检查开模进度和质量,避免出现较大的进度延迟或失误。
1. 结构件开模
2. 模具验证,试模
3. 定期检查开模进度和质量
4. 输出《综合BOM》
5. 电子元器件备料
6. 成本核算
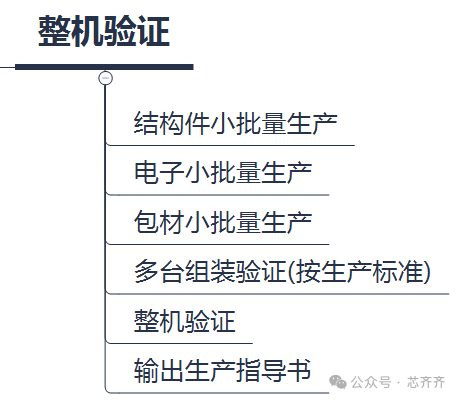
在模具进入T1阶段后就可以根据情况进行小批量的生产了,从而进行整机的综合测试。这个阶段主要是针对以下几个方面进行的测试和验证,并输出相关报告和生产指导书。
1. 验证模具的质量,结构件小批量生产,生产出来的壳体是否有问题,抗跌落或其他测试否能通过。并对出现的问题进行修复优化。
2. 对于电子开始小批量的SMT,验证PCBA的质量,总结SMT的经验和问题,并进行优化改进以及产出生产和测试的方法。
1)PCBA生产:小批量生产印刷电路板组件(PCBA),通过表面贴装技术(SMT)安装电子元器件。
3. 包材小批量生产,包装是否开始生产可视情况而定,若需要进行产品的内测,有条件的话可以进行小批量的生产。
1)小批量生产包材:按照确认的设计方案,小批量生产包装材料,包括内外包装、说明书等。
5. 撰写输出《产品生产指导书》
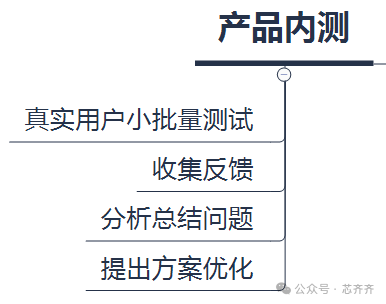
产品内测这一步是非常必要的,建议在任何情况下都不要省去。在产品研发过程中虽然会进行周密严禁的测试,但是依旧不能保证覆盖实际应用中的各种场景。
因此将以上一个流程中所生产的产品交给小规模的目标用户,去真实的场景下进行长时间的使用是可以帮助我们去发现那些我们无法覆盖到的场景和问题。
1. 真实场景用户小批量测试
2. 收集反馈,改进优化
用户使用产品和我们开发人员测试使用产品的方式是不一样的,所以通过这种方式也可以帮助我们找出产品设计中的不足,获得用户真实的使用体验,及时的对产品进行优化。
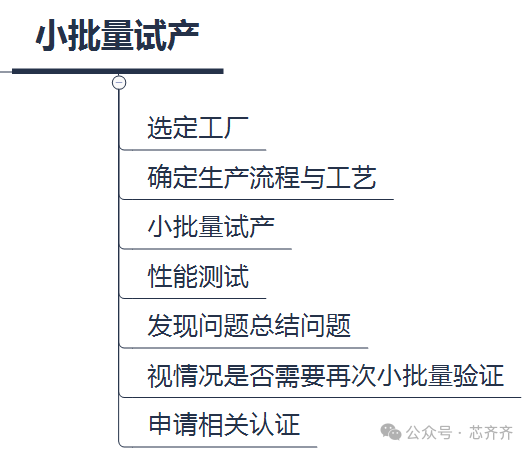
当经过用户内侧并把发现的问题进行修复验证后,产品研发阶段就正式告一段落了,接下来就要进入生产的阶段了。
开始生产的第一步是选择一个适合的代工厂,在选择时优先选择有相关产品经验且管理规范的工厂,最好相关设备都具备,可以在一家完成SMT、壳体生产加产品组装等相关流程。
如果满足不了这样的条件,那么也要选择有经验管理规范的厂子,至于SMT和壳体生产可以整合其他厂商进行合作,不过这种情况下要注意责任的划分避免出现问题后双方扯皮的事情。选厂时尽量避免那些没有经验,管理松散的小厂,不然以后问题会多了去的。
选好工厂后就要开始与工厂的工程师确定产品的生产流程和工艺了,这一步搞定后就可以开始小批量的生产了。
根据产品类型的不同,生产的数量也不尽相同,不过通常也会生产数百台产品。做这一次小批量试产的目的是为了验证产品生产流程、元器件批量加工、生产工艺和工人的能力等多方面问题,在这一步要对生产流程进行高度的关注,对过程中出现的问题进行总结分析得出解决方案。
同时对产品的成品率进行监控,如果有条件的话可以再次进行一次内测,即便不能进行内测也要多产品进行大规模的抽查使用,以便发现隐藏的问题,模拟客户受到产品的过程和体验。
若在此流程没有什么问题,那么便可进入下一步的正式量产了。此时也要开始对产品进行各方面的认证申请了。
1. 选定工厂:审厂
2. 确定生产流程和工艺
3. 小批量试产
4. 大规模的抽查使用
5. 发现问题总结问题
6. 视情况是否需要再次小批量验证
7. 申请相关认证
经过试产也就基本没有什么问题与工厂也都应该磨合好了,下面就按照生产排期进行生产即可。不过在这个过程中还是需要相关同事进行驻场监督,以免出现问题不能得到有效及时的解决。
在这里需要对产品的加工处理、员工的操作标准、以及质检的规范程度等方面进行有效的监督和保证,只有这样才可以保证产品不会出现质量问题。
在产品生产的过程中产品经理需要开始编写产品维修手册,准备相应的维修更换的部件,以备售后使用。
1. 生产流程、工艺、标准细化
2. 相关同事驻场监督
3. 生产过程质量把控
4. 成品质量把控
5. 撰写输出《产品维修手册》
6. 配备相应的维修替换部件
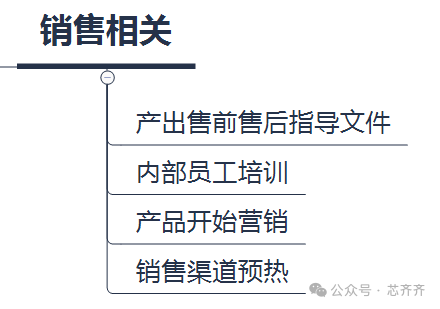
在生产过程中产品经理还有一个重要的工作要开始执行了,那就是与产品销售相关的工作。这一部分主要包括产品销售材料的制作,比如宣传文件或宣传视频等资料。
同时也要对销售同事进行培训,帮助他们理解产品在市场的定位以及自家产品的优劣势,同教授产品的使用,便于他们进行宣传和销售。
此时还要和售后、技术支持等同事进行培训,告诉他们产品使用方法和可能出现的问题以及应对的方法和话术,并对技术支持进行维修和故障诊断进行培训。
这个时候市场和销售同事就要开始对产品的营销和渠道预热等相关工作了,产品经理需要配合他们完成相应的内容。
1. 产品销售材料
2. 售前售后指导文件
3. 对销售同事进行培训
4. 对售后、技术支持等同事的培训
5. 产品营销
6. 销售渠道预热
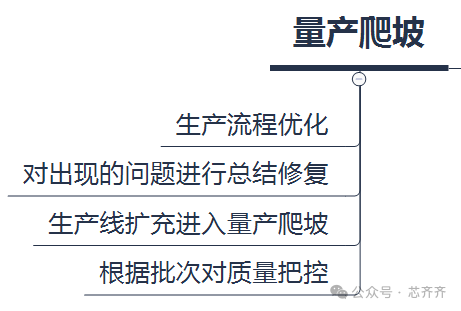
量产爬坡是通过生产流程的优化、提高员工熟练度等方法提升产品的生产速度,在规定的时间内连续大量的生产产品。这个时候需要对产品生产的过程进行全面的监控,保证爬坡的稳定和产品的质量。
当经历过这个阶段后产品就算开始稳定的出货了,此时产品经理算是完成了最重要的使命了,接下来可以松口气,投入到产品的销售和维护等相关工作中了。
1. 提升产品的生产速度
2. 全面监控
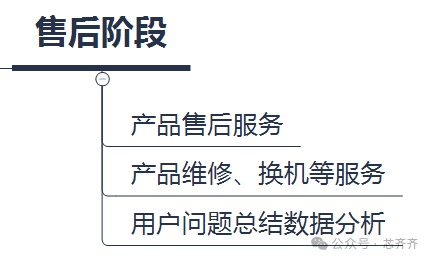
在售后阶段除非你产品问题很多,不然产品经理基本就没有太多的事情,主要是做好售后相关同事的培训工作,遇到新问题帮助解决。对于产品销售的数据和市场进行持续的关注即可。
1. 产品售后服务
2. 用户问题总结
3. 数据分析
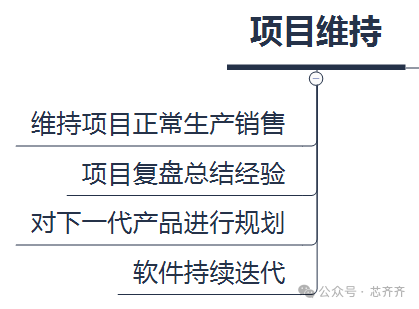
在产品的销售和生产都稳定之后基本进入维持的阶段了,此时需要适当的保持产品软件的维护和迭代,对产品进行生产排期等相关工作。
接下就需要对项目进行复盘总结了,分析在项目进行中的各项问题,以及再做项目时如何避免这些问题。
如果产品还有下一代需要启动,那么你就可以着手对下一代产品进行规划开始新的战斗了……
1. 产品软件的维护和迭代
2. 生产排期
3. 项目复盘
4. 规划下一代产品
智能硬件产品研发全流程: